Inductive touch button
QuickField simulation example
The touch button consists of the energized coil on a PCB and a metal foil. When the button is pressed the metal foil bends towards the coil. Eddy currents in the foil cause a change in the coil inductance value, which could be detected.
Problem Type
Axisymmetric problem of Stress analysis and AC magnetics.
Geometry
Given
Metal electrical conductivity 37 MS/m;
Coil current I = 0.1 mA, frequency f = 8 MHz,
Finger force f = 2 N;
Metal foil thickness 0.25 mm, Young's modulus E = 70 GPa, Poisson's ratio ν = 0.33.
Task
Calculate the inductance value change due to the foil deformation.
Solution
First the mechanical problem is simulated to calculate the deformed foil shape. Then two AC magnetic problems are simulated: with flat foil and deformed foil.
Results
Foil central part displacement is 30μm. Deformed foil profile:
Nominal coil inductance value is 622 nH. Inductance value decrement for the button pressed state is 2%.
On the picture: the deformed shape of the foil scaled 20 times, the eddy currents distribution in the foil and calculated inductance values.
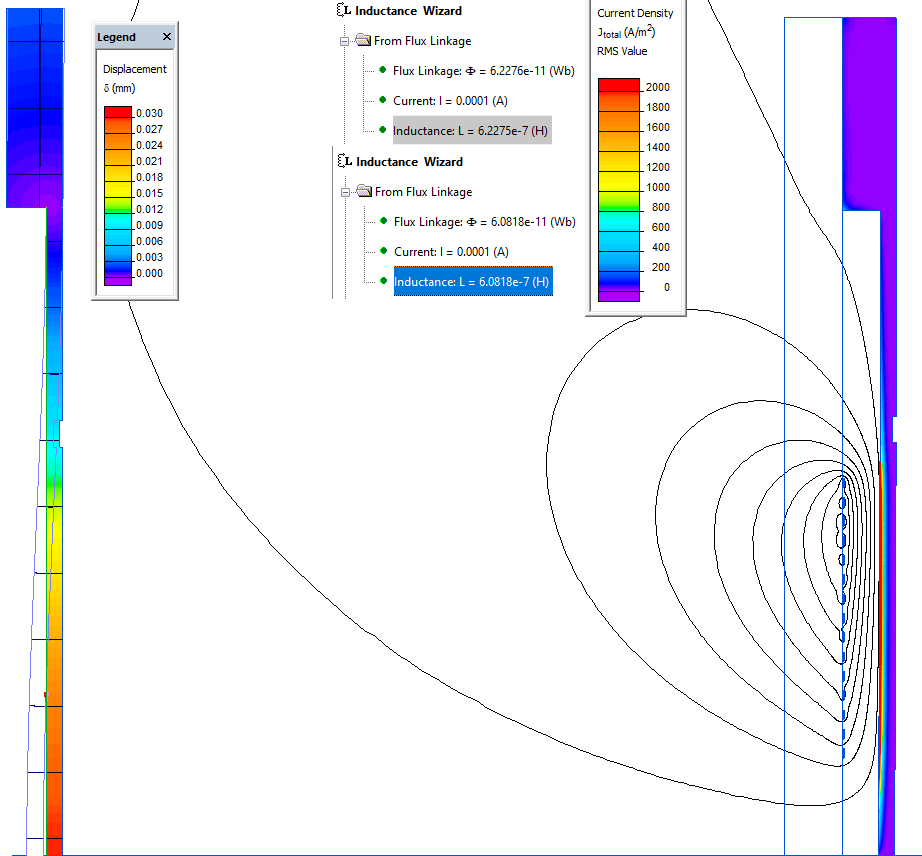
* Reference: Ben Kasemsadeh, Luke LaPointe (Texas Instruments) Inductive Sensing Touch-On-Metal Buttons Design Guide
- Video: Inductive touch button. Watch on YouTube
- Download simulation files (files may be viewed using any QuickField Edition).